Advances in PVC heat
and light stabilization
Stabilizers play a key role in the PVC industry, where the market
is driven by both regulatory and cost-performance issues. Jennifer
Markarian reviews some of the latest developments in heat and light
stabilization for PVC.
|
|
|
Both rigid and flexible PVC require an effective additive package to function,
including some combination of stabilizers, lubricants, processing aids,
plasticizers, and impact modifiers. Additives may interact, and an additive
package should be optimized for cost-performance in a given application.
Stabilizers are key components of an additive system. Heat stabilizers
are used primarily to protect the polymer during processing, but also
prevent longer-term heat degradation in the end-use. Light stabilizers
are used primarily in flexible PVC to protect the polymer from ultraviolet
light degradation. Development in stabilizers is driven by both regulatory
and cost-performance issues.
The global market for heat stabilizers, with virtually all product going
into PVC, was 500-540 million kg (1.1 to 1.2 billion pounds) worth between
$1.7 and 1.8 billion in 2003, notes Fred Gastrock, product manager for
additives at BRG Townsend, Inc., a plastics consultancy. Heat stabilizer
market growth generally follows PVC market growth with an average of 2-3%
globally. Lead stabilizers made up about half the volume and about one
third of the value, but are predicted to have little to no growth. Tin
stabilizers, with about 15% of market volume and just less than a third
of the market value, are expected to see 3% volume growth. Mixed metal
stabilizers, with about 25% of the volume and more than a third of the
market value, should grow at about 4%. Organic stabilizers have a small
piece of the market with less than $10 million in sales.
The Asia-Pacific region has the largest and fastest growing heat stabilizer
market, with about 40% of global sales. Overall, the region has an AAGR
of 4%; in China alone the AAGR is 10%. While a significant amount of additives
used in China is imported, some additive production is beginning in China,
says Mr. Gastrock. Atofina, for example, has a new facility in China producing
butyl and octyl tin stabilizers. A rare-earth co-stabilizer sourced, produced
and used in China makes up about 5% of the Chinese market, notes Mr. Gastrock.
"The Asian PVC industry appears to be adopting additive types used
in the Americas, such as tin and mixed metal stabilizers. While local
markets might accept lead-based stabilizers, the Asian PVC industry is
targeting exports that meet requirements for American applications, such
as the growing vinyl siding and profile markets," says Mark Heldt,
business manager for stabilizers at Atofina.
PVC consumed between 1.8-2.3 million kg (4-5 million pounds) of light
stabilizers in 2003, which is only about 6% of the global light stabilizer
market, comments Mr. Gastrock. Benzophenone ultraviolet absorbers (UVAs)
are the most prevalent PVC light stabilizer, followed by benzotriazole
UVAs. Light stabilizers are used primarily in flexible PVC.
Flexible PVC
Flexible PVC, used in applications such as flooring, wall covering, toys,
and coated films and fabric, typically uses barium/zinc (Ba/Zn), calcium/zinc
(Ca/Zn), or barium/cadmium (Ba/Cd) mixed metal stabilizers. Cadmium stabilizers
are no longer used in Europe, and continue to be replaced with other mixed
metals in North America. The biggest issue for flexible PVC, particularly
for flooring and wall covering, continues to be volatility. New additives
such as Akcros' Akcrostab, Crompton's Mark 9300 series, and Ferro's Therm-Chek
liquid mixed metal stabilizers have very low volatile organic compound
(VOC) levels, which reduces emissions at both the production plant and
the end-use point. The new additives also have low levels of phenols and
phenolic compounds, which are a concern in wall covering and flooring
applications for improving indoor air quality. In Europe, the trend is
to also eliminate nonyl-phenols, which may be regulated in the future.
Printability is an issue in calendered film applications such as banner
stock. Ferro has developed new stabilizer systems in which low molecular
weight material does not exude to the surface and interfere with printing.
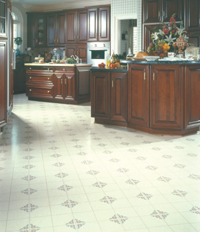
Figure 1: Flexible PVC is used in flooring. (Photo: Ciba Specialty
Chemicals)
|
The most commonly used UV stabilizers in flexible PVC are benzophenone
UV absorbers, such as Ciba® Chimassorb® 81, Crompton's MarkScreen
1413 or Cytec's Cyasorb® UV 531, and benzotriazole UV absorbers, such
as Ciba® Tinuvin® P or Crompton's MarkScreen UV-7P. "There
has been renewed interest in extending the performance and durability
of PVC beyond what is possible with traditional UV absorbers. This interest
has come primarily from producers of flexible PVC roofing membranes and
producers of PVC alloys such as PVC/ABS," notes Gerry Capocci, NAFTA
market manager for construction plastic additives at Ciba Specialty Chemicals.
Although conventional hindered amine light stabilizers (HALS) cannot perform
well with highly acidic PVC due to their basicity, new, non-basic light
stabilizers like Ciba® Tinuvin® XT 833 perform extremely well
in an acidic environment. Ciba has found that Tinuvin XT 833 gives better
durability than twice the concentration of a UV absorber in PVC. Tinuvin
XT 833 is being used in roofing membranes, which is one of the most demanding
flexible PVC applications. "We think it is possible for Tinuvin XT
833 to replace UV absorbers in flexible PVC similarly to the way traditional
HALS replaced UVAs in polyolefins several decades ago," predicts
Mr. Capocci.
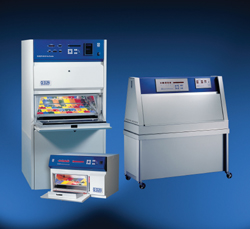
Figure 2: The QUV from Q-Panel provides reproduction
of short-wave UV, while the Q-Sun Xenon Test Chamber offers full
spectrum sunlight.
|
PVC in wire and cable
In both North America and Europe, flexible PVC in wire and cable jacketing
applications are beginning to move from lead-based stabilizers to mixed
metal stabilizers. The European vinyl industry has a voluntary commitment
called Vinyl 2010 to replace lead stabilizers with more environmentally
friendly mixed metal or organic stabilizers. The goal is to be lead-free
by 2015 and to have reduced lead consumption by 50% from 2000 to 2010.
"The challenge is in finding stabilizers with comparable cost-performance
to lead-based stabilizers. Significant development efforts have led to
mixed metal stabilizers that can offer the market a workable solution,"
says David Ankrett, business director for stabilizers at Ferro Polymer
Additives.
Rigid PVC
Rigid PVC, used in applications such as pipe, siding, and window and door
profiles, experiences higher processing temperatures and higher shear
than flexible PVC and requires more effective heat stabilizers. In North
America, rigid PVC typically contains tin-based heat stabilizers. Tin
is expected to remain the primary stabilizer system, with mixed metal
and organic stabilizers filling niches, notes Scott Chambers, North American
business director for vinyl additives at Crompton Corporation and president
of the U.S. Tin Stabilizer Association (TSA). Tin mercaptide stabilizers
have very good heat stability but poor light stability, which can be overcome
by the addition of titanium dioxide. Because of its opacity, titanium
dioxide acts as an ultraviolet light (UV) blocker in addition to being
used as a base for white pigment. Darker coloured siding and profiles,
growing in use in the U.S., cannot use titanium dioxide. Tin maleate or
tin carboxylate-based stabilizers offer better light stability but poorer
heat stability. UVA light stabilizers may be used with these to give incremental
improvements, notes Don Brilliant, PVC industry consultant. New light
stabilizers such as Ciba® Tinuvin XT833 can have a very positive contribution
to weatherability in non-tin mercaptide formulations, adds Mr. Capocci.
"New additive technology for exterior applications balances the need
for good processability and durability with weatherability," explains
Mr. Chambers. Crompton's Mark 2289, containing a tin maleate stabilizer,
is designed to prevent yellowing of light colours, particularly in the
desert-like conditions of the south-west U.S., for example. Crompton's
Mark T634 stabilizer combined with an appropriate lubricant and UV stabilizer
will minimize fading or chalking of dark colours over time in wet environments,
adds Mr. Chambers. In some products, a PVC cap layer with a higher level
of tin stabilizer is coextruded over a PVC base with a lower stabilizer
level. An alternative solution for weathering protection is to use an
inherently weatherable capstock material such as acrylic or PVC-acrylic
alloys. These capstocks are currently used most with darker colours in
the premium siding market. The North American-based Vinyl Siding Institute
plans to raise the minimum performance standards of vinyl siding over
a period of several years. This will force the industry to look at options
such as cap materials and UV stabilizers to improve weatherability, says
Mr. Capocci.
Figure
3: Lead replacement in pipes in Western Europe. (Crompton Corporation)
|
Europe, which does not have a significant vinyl siding market, currently
uses mostly lead heat stabilizers in window and door profiles. Tin stabilizers
are used in Europe only in niche applications such as clear parts. Window
and door profile applications are slowly changing from lead stabilizers
to Ca/Zn mixed metal stabilizers, since organic based stabilizers do not
meet weathering criteria, says Peter Marschalek, marketing manager at
Chemson. "Outdoor weathering tests are currently in progress with
profiles containing Ca/Zn stabilizer systems. Once these new systems are
shown capable of meeting Europe's ten-year weatherability guarantee, the
changeover from lead to mixed metal stabilizers will probably proceed
very quickly. Producers are also keeping in mind the goal of being lead-free
by 2015," adds Mr. Marschalek.
North American pipe typically uses tin stabilizers while European pipe
has traditionally contained lead-based stabilizers. As in other applications
in Europe, pipe is moving to Ca/Zn or organic stabilizers. The transition
has been slow because pipe is particularly cost-competitive in Europe,
notes Mr. Ankrett. Although the organic stabilizers do not give as white
a polymer product as lead or tin stabilizers, this has not been an issue
in Europe where pipes are typically coloured, compared to white pipes
in the U.S., comments Mr. Brilliant (see Figure 3).
New stabilizer systems are being marketed for rigid PVC foam, which is
growing in construction applications, comments Mr. Chambers. New stabilizer
packages are also being marketed to the wood-plastic composite (WPC) market.
While olefin-based WPC are well established in North America, PVC-based
WPC are also beginning to grow, notes Mr. Chambers. Chemson has developed
both lead and lead-free stabilizer packages for the new and growing European
wood-PVC composite market. In Europe, profiles typically contain 20-30%
PVC and are primarily used in building applications, notes Mr. Marschalek.
Other developments in rigid PVC stabilizers are additive packages designed
for improved processing and higher profile production speeds. For example,
Crompton's specialized tin stabilizer platform includes the Mark 2900
series packages to reduce plate-out in profile and pipe production and
the Mark 2200 series packages that eliminate chatter in high speed, window
profile production.
As the vinyl processing industry has improved process and dosing control,
users would like to save costs by lowering stabilizer levels to the minimum
necessary for performance. Atofina recently introduced the Thermolite
140 tin stabilizer formulation with lower tin levels targeted to meet
both economic and performance requirements for siding substrates, explains
Mr. Heldt.
Testing of PVC heat and light stability
Testing of polymer stability examines either process stability or heat
and light stability of the end-use product. Process stability is typically
measured in a static oven test, a dynamic torque rheometer test, or a
process-simulation such as milling. These tests gauge colour development
and physical properties over time as a measure of how well the additive
package protects the polymer from degradation. Weathering or light stability
is tested either in a laboratory weathering chamber that provides accelerated,
simulated exposure or in actual outdoor exposure.
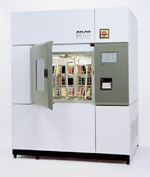
Figure 4: The Ci5000 from Atlas Material Testing Technology.
|
In simulated weathering, polymer test pieces are placed in a laboratory
weathering chamber and exposed to light from xenon arc or fluorescent
UV lamps. Xenon arc light sources produce UV, visible, and IR light; optical
filters can be used to limit the spectrum. Moisture can be added through
humidity control or water spray. Experts from Atlas Material Testing Technology
say that xenon arc tests have better correlation with outdoor weathering
tests. The most appropriate test and light source depends on the material
and its failure mode, says Catherine Gadomski, international marketing
manager at Q-Panel. For vinyl siding, fluorescent UV systems provide a
more realistic simulation because moisture can be added through condensation
on the polymer part. "Colour stability in vinyl siding has much to
do with moisture levels, temperature, and UV rays. Moisture in outdoor
applications comes primarily from condensation on the part," explains
Ms. Gadomski. Required test protocols, including light source, vary by
country and by application. For example, weathering test guidelines for
PVC window profiles typically ask for extended testing periods equivalent
to five years, with specific conditions such as moderate or extreme climate,
notes Atlas. Five years outdoor weathering is equivalent to 4000 to 6000
hours on a xenon instrument.
While weatherometer testing is useful for comparing relative performance
of various additive packages and may be sufficient for approval in some
applications, other applications require outdoor weathering testing for
approval. New chemistries are typically tested in two or more different
environments. Hot, humid Florida and the Arizona desert are considered
primary benchmarks. During a weathering experiment, polymer colour and
physical property retention, either impact strength for rigid PVC or tensile
properties for flexible PVC, are monitored. Chalking or whitening of the
part surface can be observed in outdoor weathering tests. Chalking may
occur in humid environments, and is particularly obvious on darker-coloured
parts. The North American Vinyl Siding Institute (VSI) standards currently
call for two years of outdoor weathering in subtropical, desert, and northern
industrial climates. VSI is considering an accelerated, simulated ageing
program that would grant temporary certification while outdoor testing
results were pending.
Plastics
Additives & Compounding© Copyright 2005, Elsevier Ltd
|